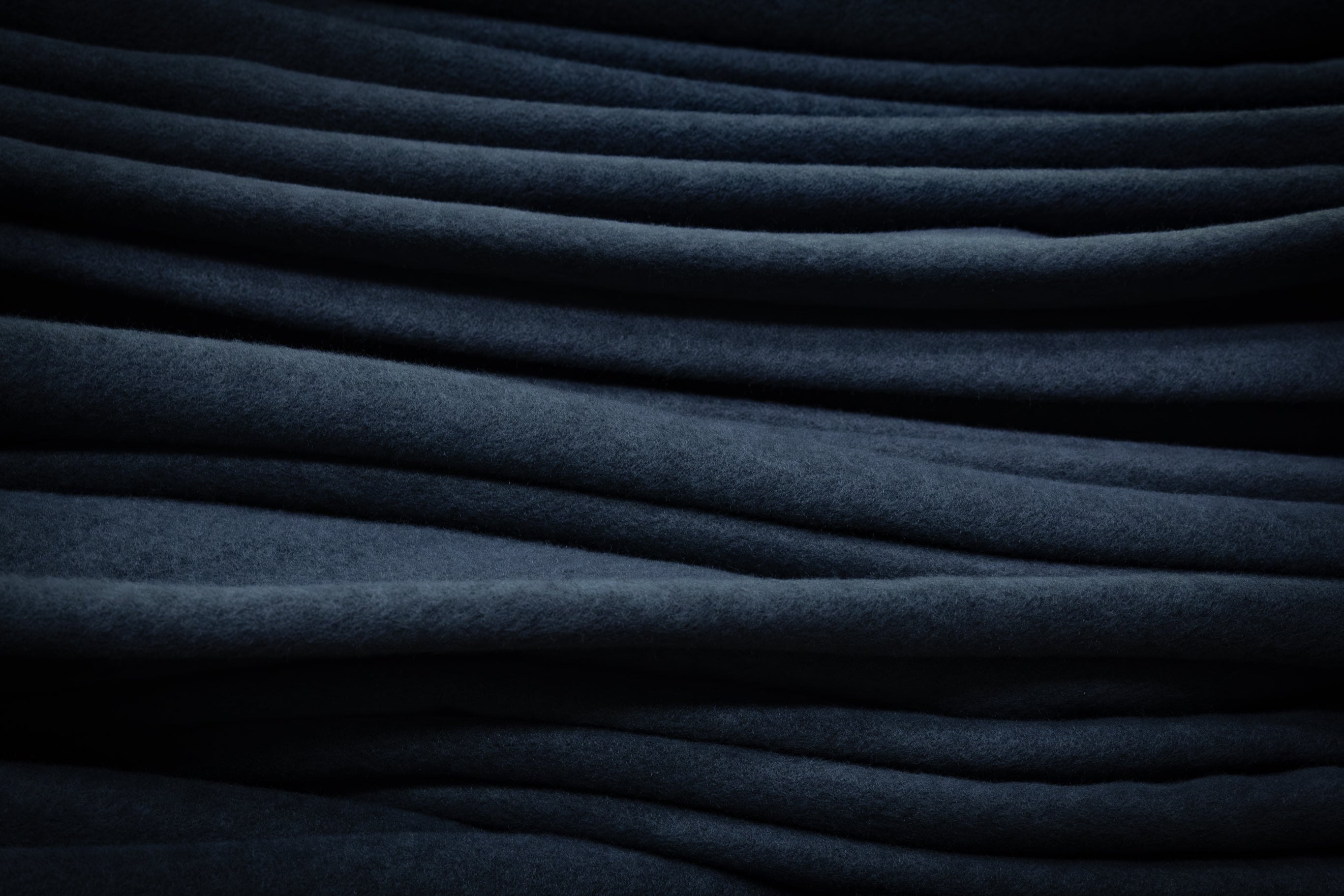
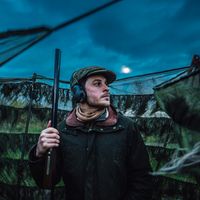
A trip to Italy | What sets Schöffel fleece apart from the rest?
We visit Pontetorto, the revered textiles company in Tuscany, to learn more about how our premium Tecnopile fleece is made...
Two-thousand-three-hundred-and-fifty needles bind the raw yarn… Four hours of prep precede the dyeing… Temperatures of 130C drive the dye into the fibres… There are eight stages of brushing and shearing... The fabric is heat set at 180C… Ninety-three per cent of the water used in the process is recycled... Finally, the finished product must pass four stringent tests in the Pontetorto lab…
Such stats allude to the thorough and meticulous process used to craft Schöffel’s Italian-milled fleece. But what do they really mean? Why are they important? And how do they translate to a premium-quality fleece that is warm, soft, durable and – we believe – the finest in the world?
The journey from raw yarn to finished fleece, ready to be cut and sown, is eye opening. And it’s central to what makes the likes of our Oakham and Lyndon Fleece Gilets what they are. So, we visited our friends at Pontetorto in Tuscany, Italy, to document that journey and show you why the fleece they produce exclusively for Schöffel Country stands apart from the rest…
Designed in Britain, milled in Italy
The ethos of the companies we work with is very important to us at Schöffel Country: a commitment to unwavering quality is a must, an openness to innovation is essential, and attention to sustainability holds great weight.
Pontetorto, the Italian textiles company which produces the fleece for many of our products, is a prime example of one such that delivers on all fronts. It’s for good reason we entrust them with producing the fabric for the products in our esteemed fleece collection.
Located in the province of Prato in the Tuscany region of Italy – an area synonymous with textiles since the Middle Ages – Pontetorto has a pedigree of excellence and, much like Schöffel, strikes a sterling balance between tradition and modernity.
Brought to be by the Banci family in 1952, Pontetorto first established itself as a specialist in the woollen field and was well known for its expertise in the finishing of classic velours for the manufacture of coats. It has since, however, put its breadth of experience to use in the development of high-quality fleece.
“Nineteen-eighty-five was the turning point,” Elena Banci, whose father founded the company, told us when we visited the Pontetorto factory earlier this year. “That’s when we started to produce high-performance fleece for the outdoor sports sector.”
The pioneering fleece was called Tecnopile. “It put the company on the world stage,” said Elena, matter of factly. She explained how, over the years, different weights and textures have been added to the Tecnopile range to suit different markets. Some lines, such as those used in Schöffel fleece gilets, are produced exclusively for one brand, meaning our fleece is not only milled in Italy, but it is truly one of a kind.
How is Schöffel fleece made?
Jet-dying, pressing, brushing, shearing and steaming are all crucial to the feel and longevity of our fleece. Every step has been honed at Pontetorto over decades; painstaking attention to detail during each of these stages improves the hardwearing nature of the fabric, while ensuring its colourfastness and reducing its susceptibility to shrinkage. That’s before the quality assurance work in the labs – for pilling, snagging and the like.
Our visit to Pontetorto earlier this year reminded us once again just how much thought goes into the production of our premium fleece. It’s a journey best described in pictures…
The fleece-making process – in six steps
Achieving the correct colour for the dyes is both a science and an art. Here, a robot, under the control of a lab technician, concocts small colour samples produced to ultra-fine tolerances before a recipe for a particular colour is rolled out to production. This translates to consistency in colours from one run to the next. So, when we say our fleece is ‘Navy, ‘Dark Olive’ or ‘Claret’, we can do so with absolute confidence from one year to the next.
Using 2,350 needles, the cutting-edge circular knitting machine binds the raw polyester yarn into a continuous tube of cloth. This is carefully supervised; the intricacy of the process ensures strength and uniformity of the base material.
In the dye house, the jet dying machine is loaded with the raw fleece material, where it is subject to high pressures and temperatures of 130C which drives the dye into the fleece fibres, ensuring excellent colourfastness. Ninety-three per cent of the water used at Pontetorto is recycled.
To achieve the characteristics for which premium microfleece is known, the dyed and dried fabric is brushed with ultra fine mechanical bristles. This lifts the microfibres of the material in preparation for shearing, whereby a precision blade cuts the raised fibres. This process is repeated four times on each side of the fabric. The result: a super-smooth fleece with a structure comprising air pockets between the threads that make it lightweight but very warm and able to retain its look and shape while offering incredible comfort.
After brushing and shearing, the fabric passes through the heat-set machine, which helps to prevent further shrinkage when washing. This is the final stage before inspection and testing.
In the lab, the fleece must pass a series of tests. Here, Chiara performs the tests for pilling and snagging, colourfastness, and water repellency, to ensure the fleece will stand up to the demands of everyday life, retain its original colour well, and resist water. Only if these tests are passed does the fleece get the Pontetorto seal of approval.
Read the story of our iconic fleece gilet here.